1. CNC machines
Eg:- CNC Laser-Cutting Machine
A CNC laser cutting machine is a computer-controlled device that uses a focused beam of light to cut or engrave materials. The laser beam is typically generated by a CO2 or fiber laser and can be incredibly precise, making it ideal for creating complex shapes and designs. The CNC (Computer Numerical Control) part of the name refers to the fact that the machine is controlled by a computer program that tells it exactly where to move the laser beam.
CNC laser-cutting machines are important for several reasons,
They can cut incredibly precise shapes and designs, even with intricate details.
They can work with a wide variety of materials, including metal, wood, plastic, glass, and even leather.
They can cut materials much faster than traditional tools, such as saws or drills.
They can produce identical cuts and designs over and over again.
They create very little waste material, which is good for the environment.
CNC laser cutting machines are used in a wide variety of industries,
They can cut parts for cars, airplanes, and other machines.
They can create delicate rings, pendants, and other jewelry pieces.
They can cut out logos, letters, and other designs for signs.
They can create furniture parts, decorative pieces, and even toys.
They can cut and shape precise components for medical devices.
can cut intricate designs and patterns for clothing and accessories.
They can cut decorative elements and custom architectural components.
Types of Laser Cutting Machines,
o CO2 Lasers
CO2 lasers, once the most prevalent type, are now being overshadowed by the advancements in fiber laser technology. A CO2 laser comprises a long, vacuum-sealed tube filled with gas, predominantly carbon dioxide with some nitrogen. Electrifying the tube excites the gas molecules, generating strong light. Mirrors and a focusing lens then concentrate the light, allowing the laser to cut through various materials through thermal separation.
CO2 lasers excel in sheet metal fabrication, offering a distinct advantage over fiber lasers in edge quality, particularly on metal thicker than 0.25 inches. They are renowned for their affordability, though newer technologies are gradually replacing them.
o Fiber Lasers
Operating on a principle similar to fiber optic lights, fiber lasers channel light through a coated glass tube with unique reflective properties. This amplifies the light's strength as it bounces along the tube. The nature of fiber optics enables the laser to achieve a finer diameter, facilitating high-detail cutting and making low-wattage fiber lasers ideal for engraving projects. Fiber lasers are well-suited for reflective materials like metal, and their high power variants are capable of cutting through substantial thicknesses of material. Despite being large and costly, these machines boast minimal maintenance requirements and few components that might need replacement or adjustment.
o Neodymium lasers
Neodymium lasers often abbreviated as Nd: YAG lasers due to their most common crystal material, stand out as versatile workhorses within the laser cutting and engraving world. While not as ubiquitous as CO2 or fiber lasers, their unique properties shine in specialized applications where unmatched precision and control are paramount. At the core of a neodymium laser lies the eponymous neodymium (Nd) ion, nestled within a Yttrium Aluminum Garnet (YAG) crystal. When pumped with intense light, typically from flashlamps or diodes, the Nd ions become excited, storing energy like tiny batteries. This stored energy is then released in a precise burst, creating a highly focused beam of light at a specific wavelength (around 1064nm). Think of it as a microscopic slingshot, propelling light with exceptional accuracy and coherence.
Sensory Inputs of the CNC Laser Machine
· Axis Encoders
These act as the machine's "eyes," constantly monitoring the position of the laser head along the X, Y, and Z axes. Think of them as microscopic rulers, ensuring the head moves with pinpoint accuracy on the pre-programmed path.
· Material Height Sensor
Imagine cutting a cake without knowing how thick it is. The material height sensor acts as the "ears" of the machine, determining the distance between the laser head and the material. This crucial information allows the machine to adjust its focus and power output for optimal cutting results.
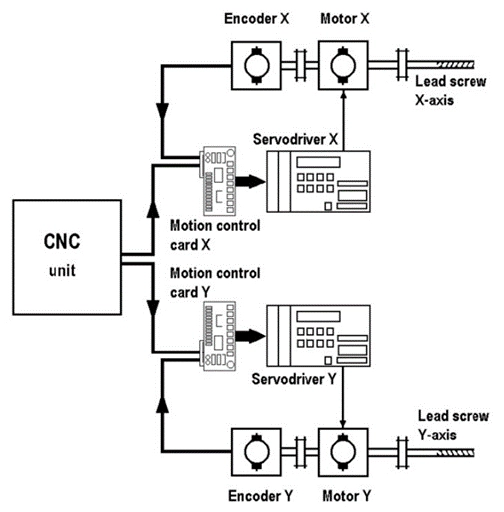
· Laser Power Monitor
Just like a chef adjusting the heat on a stove, the laser power monitor keeps tabs on the laser beam's intensity. This ensures consistent cutting quality across different materials and thicknesses.
Actuators of the CNC Laser Machine
· Axis Motors
These workhorses power the movement of the laser head along the X, Y, and Z axes. Think of them as powerful engines, guided by the precise data from the encoders, to meticulously follow the cutting path.
· Laser Power Control System
This system adjusts the laser beam's intensity based on the material and desired outcome. Imagine a dimmer switch for the laser, ensuring different materials receive the perfect amount of "heat" for clean cuts.
· Exhaust System Fan
This vital component drives the exhaust system, pulling away fumes and debris created during the cutting process. Think of it as a powerful vacuum cleaner, keeping the work area clean and safe.
Techniques to improve the productivity or product quality of the machine
1. Advanced Nesting Algorithms
Nesting algorithms minimize material waste by fitting various shapes onto a single sheet. Advancements like genetic algorithms and simulated annealing can further optimize material usage, boosting both productivity and cost-effectiveness.
2. Adaptive Laser Power Control
Dynamically adjusting laser intensity based on material thickness, desired cut finish, and even real-time feedback from sensors. This ensures consistent quality across varying materials and thicknesses, minimizing scrap and rework.
3. Multi-Axis Cutting
While most CNC laser machines operate on two axes (X and Y), adding additional axes unlocks a new dimension of creativity and efficiency. Imagine carving intricate 3D sculptures or cutting complex, multi-faceted shapes with unparalleled precision. This technology opens doors to new applications and enhances design possibilities.
4. Predictive Maintenance
Instead of waiting for breakdowns, we can anticipate them. By analyzing sensor data like vibrations, temperatures, and power consumption, predictive maintenance algorithms can identify potential issues before they arise. This proactive approach minimizes downtime, maximizes machine uptime, and ensures consistent production schedules.
5. Beam Shaping and Advanced Optics
Modern techniques can be applied to laser beams, shaping them into specific patterns or manipulating their wavelength. This allows for targeted cutting, minimizing heat-affected zones and enabling intricate features on delicate materials.
2. Industrial Robots
Eg:- Cartesian robots
Unlike their articulated cousins with rotating joints, Cartesian robots prioritize pure linear motion. Picture a three-dimensional coordinate system, with the X, Y, and Z axes forming the guiding framework. Each axis is powered by a separate prismatic joint, essentially a long, sturdy slide mechanism. Imagine three powerful rulers, sliding on their tracks to precisely position the end effector (think of it as the robot's "hand") in any point within the designated workspace.
Applications
· Assembling electronics, pick-and-place operations, laser cutting and engraving, and material handling are just a few examples. Imagine robots building intricate circuits, transferring delicate parts, or carving intricate designs with a laser's precision.
· Palletizing, sorting, and loading/unloading tasks are perfectly suited to Cartesian robots' strength and accuracy. Imagine automated packing lines ensuring perfect pallet assembly or robots effortlessly loading trucks with optimal efficiency.
· From handling delicate fruits and vegetables to processing ingredients and packaging finished products, Cartesian robots enhance hygiene, consistency, and productivity. Imagine robots gently picking ripe apples or precisely filling bottles with beverages.
· By incorporating AI and machine learning, Cartesian robots can autonomously optimize their movements, adapt to changing environments and even self-diagnose potential issues. Imagine robots continuously learning and improving their performance, taking automation to a whole new level.
Advantages of Cartesian robots
With independent linear movements, Cartesian robots achieve exceptional accuracy and consistency. Imagine placing microscopic components with pin-point precision or stacking pallets perfectly every time.
With fewer moving parts compared to articulated robots, Cartesian robots are less prone to wear and tear, leading to reliable operation and minimal downtime. Think of a well-built workbench instead of a complex contraption, demanding less maintenance and offering unwavering stability.
From miniature desktop units to massive gantry systems, Cartesian robots come in various sizes and configurations, adapting to diverse tasks and workspace requirements. Imagine scaling the same basic design to handle delicate watchmaking or heavy metal manipulation.
The simpler design and construction translate to a generally lower cost compared to complex articulated robots, making them an accessible option for a wider range of applications. Think of getting more bang for your buck without sacrificing performance.
Working principle
The core strength of a Cartesian robot lies in its prismatic joints, also known as linear actuators. These act like invisible strings, pulling or pushing the robot's different sections along three designated axes,
X-axis: Determines movement to the left and right, akin to a dancer sliding sideways.
Y-axis: Controls movement forward and backward, as if gliding across the stage.
Z-axis: Dictates vertical movement, similar to reaching upwards or bending low.
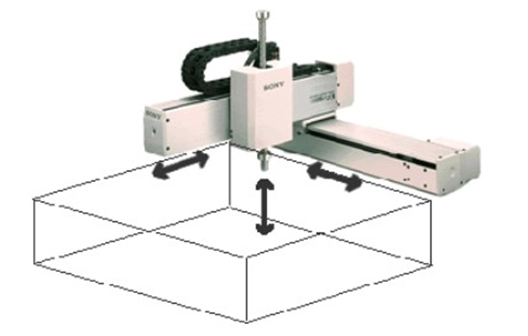
Each axis houses its own dedicated actuator, commonly powered by,
Servomotors: These offer precise control and positioning, ideal for intricate tasks.
Pneumatic cylinders: Powerful and fast-acting, perfect for heavy load handling.
Rack and pinion drives: Combining gear technology with linear motion, ensuring smooth and efficient movement.
· The Control System
This brain of the operation receives instructions, often programmed via computer software, and converts them into precise signals for each actuator. These signals dictate.
Speed and direction: How fast and in which direction each axis should move.
Position and coordination: Ensuring all axes move in sync to reach the desired endpoint.
Sensor feedback: Incorporating data from sensors, like encoders, to monitor and adjust movements for high accuracy.
Mounted on the tip of the Z-axis lies the end effector, the robot's versatile "hand." This customizable tool can be anything from a simple gripper for grasping objects to a laser head for intricate cutting or a spray nozzle for painting. The possibilities are endless, limited only by imagination and application.
With the stage set, the control system issues commands, guiding the actuators to pull and push the various sections along their corresponding axes. The end effector, meticulously controlled by this coordinated movement, dances across the workspace, performing its designated task with unwavering precision. Whether it's assembling circuit boards or stacking pallets, the robot seamlessly executes its program, leaving no room for error or improvisation.
Techniques to improve the productivity or product quality of the machine
Modern Cartesian robots incorporate exciting advancements, enhancing their capabilities and flexibility,
Multi-axis configurations: Adding additional axes expands the robot's reach and opens doors to complex manipulation.
Sensor integration: Incorporating vision systems, pressure sensors, and force feedback allows for real-time adjustments and intelligent interaction with the environment.
Collaborative robots (cobots): Designed for safe interaction with humans, cobots bring automation closer to the frontline, fostering productive human-robot partnerships.
Motion system upgrades: Investigate faster motors, lighter materials, or improved drive mechanisms like linear rails or ball screws to reduce cycle times and increase speed.
End-effector optimization: Design or choose a gripper or tool that better suits the specific task, allowing for faster or more secure handling of objects.
Maintenance and calibration: Implement regular maintenance schedules and automated calibration routines to ensure consistent performance and prevent unexpected downtime.
3. Molding machines
Eg:- Injection molding machine
An injection molding machine is a high-tech powerhouse that shapes molten plastic into countless products we encounter daily.
Parts of the Injection molding machine
Clamping Unit - Like a giant vise, it holds the mold shut with immense force while molten plastic fills the cavity.
Injection Unit - The heart of the machine, it melts plastic pellets and injects them into the mold under high pressure. This unit consists of a heated barrel and a rotating screw that mixes and kneads the molten plastic.
Mold - The canvas for the plastic masterpiece, it's a precisely crafted cavity that defines the final shape of the product.
Control System - The brain of the operation, it monitors and regulates everything from temperature and pressure to injection speed and cycle times.
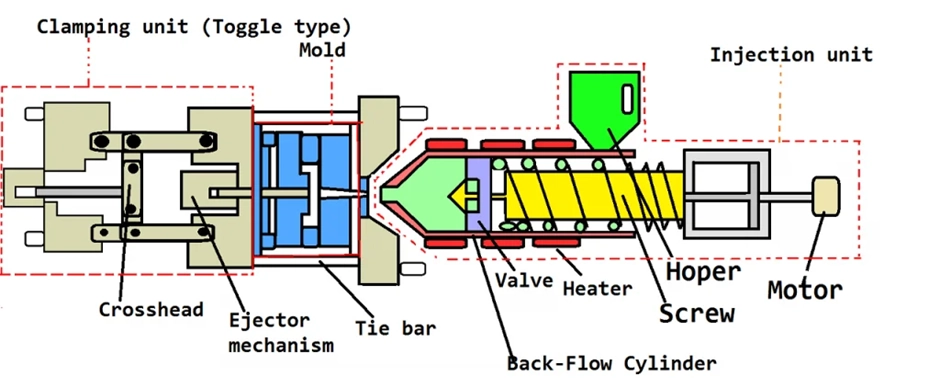
The Process in the machine
I. Mold Clamping - The clamping unit firmly locks the mold halves together, creating a sealed cavity.
II. Plastic Injection - Molten plastic, driven by the rotating screw, surges through a heated nozzle and into the mold cavity under high pressure.
III. Cooling and Solidification - The mold acts as a cooler, rapidly solidifying the plastic into its desired shape.
IV. Ejection and Cycle Repeat - Once solidified, the mold opens, and ejector pins push the finished part out. The mold then closes, and the cycle starts anew, ready to breathe life into the next plastic creation.
Applications
· Packaging
Bottles, tubs, containers, and other packaging solutions benefit from the lightweight, durable, and customizable nature of injection-molded plastics.
· Automotive
From car dashboards and interior panels to lightweight, fuel-efficient parts, injection molding plays a crucial role in modern automobiles.
· Electronics
Phone casings, circuit boards, and other electronic components rely on the precision and reliability of injection molding for flawless functionality.
· Medical
Sterile syringes, intricate surgical instruments, and even biocompatible implants benefit from the hygienic and precise nature of injection molding.
Sensors
· Temperature Sensors
Thermocouples and infrared sensors strategically placed in the barrel, nozzle, and mold cavity meticulously track the temperature of the molten plastic, ensuring optimal processing and preventing overheating.
· Pressure Sensors
Piezoelectric and strain gauge sensors monitor the pressure in the injection unit, mold cavity, and hydraulic lines, ensuring proper injection force and preventing defects like voids or flash.
· Position Sensors
Encoders and limit switches track the movements of the clamping unit, injection unit, and ejector pins, ensuring precise positioning and preventing collisions or malfunction.
· Melt Flow Sensors
These specialized sensors monitor the flow rate and viscosity of the molten plastic inside the barrel, providing valuable insights for process optimization and defect prevention.
Actuators
· Hydraulic Actuators
Powerful pistons and cylinders powered by hydraulic fluid drive the clamping unit, injection unit, and ejector pins, generating the immense forces needed for molding and part ejection.
· Electric Servo Motors
These precise and energy-efficient motors control the movements of the injection unit and other critical components, enabling precise control and rapid cycle times.
· Proportional Valves
These sophisticated valves precisely regulate the flow of hydraulic fluid and compressed air, allowing for fine-tuned control of pressure and machine movements.
Techniques to improve the productivity or product quality of the machine
Modern injection molding machines often employ additional sensors and actuators,
· Vision Systems
Cameras integrated into the machine can inspect parts for defects or verify proper positioning.
· Robot Arms
Automated robots can handle parts, load molds, and perform other tasks, increasing efficiency and reducing human intervention.
4. Printing machines
Eg:- Inkjet Printers
Inkjet printers transform digital dreams into tangible realities, one tiny droplet at a time.
Parts of the Inkjet Printers
Data Input and Processing
· Computer Connection: You send your digital files (PDFs, images, text) to the printer via USB, Wi-Fi, or Bluetooth.
· Control Panel: This interface lets you navigate menus, select settings, monitor ink levels, and initiate print jobs.
· Raster Image Processor (RIP): This crucial brain translates your digital file into instructions for the printing mechanism, breaking it down into a pixelated map with specific color values for each droplet.
Printing Mechanism
· Ink Cartridges: These house the liquid ink for each color (CMYK) and may offer specialty inks like metallics or white. Some printers use individual cartridges for each color, while others have combined cartridges.
· Print Head: This assembly houses the nozzles (usually numbering in the hundreds or thousands) and piezoelectric crystals that precisely eject ink droplets onto the media.
· Ink Supply System: This includes tubes and pumps that deliver ink from the cartridges to the print head, ensuring consistent flow and preventing blockages.
Media Handling
· Paper Tray: This holds the paper you want to print on. Some printers may have additional trays for different paper sizes or types.
· Feeder Mechanism: This automatically pulls paper from the tray and feeds it into the printing path.
· Roll Paper Feeder (Optional): Some printers allow continuous printing on rolls of paper instead of sheets.
· Output Tray: This catches the printed pages as they exit the printer.
Supporting Components
· Waste Ink Tank: This collects used ink from the cleaning process and cartridge purges.
· Cleaning System: This keeps the print head and other components clean to prevent clogs and ensure high-quality printing.
· Power Supply: This provides the electricity needed to run the printer.
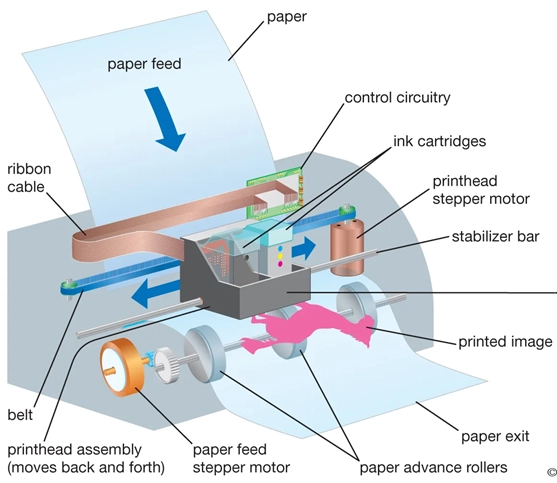
Sensors
· Cartridge Sensors: These intelligent chips embedded in each ink cartridge track ink levels, alerting the user when refills are needed and preventing printing mishaps due to empty cartridges.
· Paper Sensors: Strategically placed sensors detect the presence of paper in the tray and its type, ensuring proper feeding and preventing jams or wasted ink.
· Print Head Position Sensors: These precise sensors track the movement of the print head along the carriage, guaranteeing accurate droplet placement and preventing misalignments.
· Encoder Sensors: These rotary wonders monitor the movement of the paper feed rollers and carriage, ensuring consistent speed and paper advancement during printing.
Actuators
· Piezoelectric Actuators
Nestled within the print head, these tiny crystals convert electrical pulses into precise ink droplet ejections, controlling the size and direction of each microscopic brushstroke.
· Stepper Motors
These controlled motors drive the movement of the print head carriage along the rail, ensuring accurate positioning for each pass and flawless image creation.
· Paper Feed Motors
These powerful motors control the rollers that pull paper from the tray and feed it through the printing path, maintaining smooth and consistent movement.
· Solenoid Valves
These fast-acting valves regulate the ink flow from the cartridges to the print head
Techniques to improve the productivity or product quality of the machine
· Research and development into alternative inkjet technologies like continuous inkjet or drop-on-demand with higher firing frequencies could significantly increase printing speeds.
· Implement faster and more efficient RIP processors to handle complex print jobs and large files quicker, reducing processing time and waiting periods.
· Develop intelligent ink cartridge systems that automatically detect low ink levels and refill cartridges on the fly, minimizing downtime and interruptions.
· Improve paper feeding mechanisms and tray designs to avoid jams and misfeeds, ensuring smooth paper flow and faster printing.
· Develop next-generation print heads with even smaller nozzles and better droplet control for ultra-high resolution printing and sharper details.
· Implement sophisticated color profiling and calibration techniques to ensure accurate and consistent color reproduction across different printers and media.
5. Packaging machines
Eg:- Conveyors
Conveyors serve as the backbone of modern packaging machines, providing a seamless and automated way to transport products throughout the packaging line. They eliminate manual handling, reducing the risk of errors and increasing the overall speed and efficiency of the packaging process.
The primary goal of conveyors in packaging machines is to ensure a smooth and continuous flow of products from one stage of the packaging line to another. This not only optimizes the use of space but also facilitates the integration of various packaging components, such as fillers, sealers, and labeling machines, into a cohesive and synchronized system.
Types of Conveyors
· Belt Conveyors: The workhorses, featuring continuous belts traversing rollers, ideal for conveying large volumes of products over long distances.
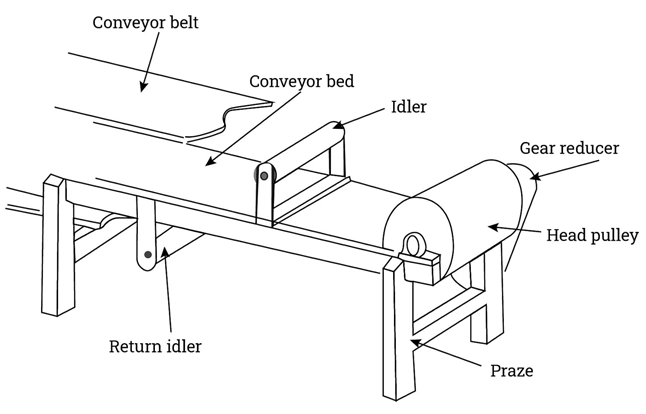
· Chain Conveyors: These sturdy performers use chains with attached slats or platforms to handle heavier items or navigate inclines.
· Roller Conveyors: Ideal for lighter loads, these utilize rotating rollers to gently move products, often seen in sorting or inspection stations.
· Spiral Conveyors: These space-saving wonders elevate products vertically while conveying them horizontally, perfect for multi-level operations.
Conveyor movement relies on three key elements,
· Drive Unit: An electric motor or hydraulic system responsible for generating power.
· Transmission System: Gears, pulleys, or chains transfer the power from the drive unit to the conveyor mechanism.
· Conveyor Mechanism: The actual moving component, be it the belt, chain, rollers, or spiral, depending on the type of conveyor.
Conveyor performance is further honed by additional equipment,
Tensioners: Maintain proper belt or chain tension for smooth movement and prevent slippage.
Guides: Keep the conveyor mechanism on track and prevent misalignment.
Sensors - Monitor product flow, track position, and detect jams, triggering adjustments to maintain smooth operation.
· Photoelectric Sensors
Photoelectric sensors are commonly used to detect the presence or absence of products on the conveyor belt. They rely on the interruption of a light beam to signal the presence of an object, enabling precise control of product movement.
· Proximity Sensors
Proximity sensors are employed to measure the distance between objects on the conveyor. This information aids in maintaining optimal spacing between products, preventing collisions and ensuring a smooth transition from one processing stage to another.
· Load Cells
Load cells integrated into conveyors provide accurate weight measurements of products. This is crucial for packaging applications where precise weight control is essential for compliance with regulations and ensuring the integrity of the packaged products.
· Barcode Scanners
Barcode scanners are utilized for identifying and tracking products on the conveyor. This technology facilitates accurate sorting, and labeling, and ensures that each product is directed to the correct packaging station.
· Vision Systems
Vision systems use cameras and image processing to inspect products for defects or irregularities. This enhances the overall quality control of packaged items, reducing the likelihood of faulty products reaching consumers.
Actuators - Pneumatic or hydraulic cylinders that adjust belt speeds, roller angles, or divert products to specific pathways.
· Motorized Drive Systems
Actuators in the form of motorized drive systems are responsible for the controlled movement of the conveyor belt. They determine the speed and direction of the conveyor, ensuring a continuous and consistent flow of products.
· Solenoid Actuators
Solenoid actuators are integral in sorting and diverting products based on predetermined criteria. They operate quickly and with precision, ensuring that each product is directed to its designated destination on the packaging line.
· Linear Actuators
Linear actuators are employed for adjusting the incline or decline of specific conveyor sections. This feature allows for customization of the conveyor system, accommodating changes in elevation within the packaging facility.
Techniques to improve the productivity or product quality of the machine.
· Analyze production flows and adjust belt speeds for maximum efficiency while minimizing bottlenecks.
· Invest in low-friction materials for belts and rollers, ensuring smooth movement and reducing energy consumption.
· Implement intelligent systems that automatically route products to designated paths, eliminating manual interventions and delays.
· Utilize modular conveyor sections for easy reconfiguration and expansion, adapting to changing production needs.
· Implement sensors and AI-powered maintenance systems to monitor conveyor health and prevent downtime through proactive interventions.